Welding Technology
Process optimization in welding technology and production engineering
When it comes to process optimization in welding technology, we are your contact. From the monitoring of highly iterative prototype processes and single-part production through ramp-up phases to series processes, we provide you with advice and support backed by our long-standing experience and our specialists.
Production Engineering
Reduction of rejects in running production or the perfect entry into series production? Due to our experience in the automotive sector we are able to actively support you, whether in the field of Powertrain, Body in White or Interior and Safety.
Prototype manufacturing:
The sector of prototype manufacturing is fascinating and demanding. Physically manufacturing parts and components for the first time requires the identification of a process and the development of a suitable process landscape. Our experience shows that it is often not production-related obstacles that have to be overcome, but design-related difficulties: Accessibility of the joining point, fitting accuracies of the joining partners and the resulting gap dimension and/or the periphery of the joining technology.
Especially in this early phase of a product, it is often forgotten that clamping elements and hold-down devices not only serve to align the components, but also have to withstand enormous forces due to heat distortion during the welding process. Fitting accuracy and gap dimensions must always be in harmony with the clamping technology and fit the joining process to be used.
We support you at the earliest possible stage of development to ensure that the correct process and process landscape is followed. Upon request, we produce
3D prototypes, for example to adapt fixtures and optimize product details. These can then either serve as pure show-off models or be established in the process if the mechanical / physical conditions allow.
Single-part production:
Batch size 1 is usually associated with high individual part costs. High costs due to the fact that the basic cost drivers in the welding process, such as clamping technology, are not amortized by high quantities. So everything has to fit! A lot can be steered in the right direction before welding production starts. Alongside clamping and measuring technology, the three core areas of welding technology naturally also play the main role here: manufacturing technology, materials technology and design technology.
The welding-compatible design of components is an essential requirement for achieving a safe connection. We gladly assist you with the layout under special consideration of the welding safety. This involves the weld-compatible design of components with the aid of welding design principles, the calculation of weld seams and seam volumes, and the investigation of the behavior of weld seams under different stresses.
The material processing passes through complex phases as a result of the process. We consult on the selection of base or filler materials to avoid defects. Concerning hot cracking, particularly in austenitic stainless steels, even minor changes can achieve excellent results.
Also in this area, we hold a vast experience, which is purposefully utilized for the solution of your tasks and problems.
Benefit from our expert advice on the selection of welding consumables to get the maximum out of your base material.
Start of series production (Ramp-up)
We adapt to the highly iterative cycles during the ramp-up phase and work with you to develop sustainable, long-term optimization solutions. The bridge between individual parts from prototype development via small series to series production is built here during the ramp-up.
On the detailed way to final acceptance and the fulfillment of the customer’s requirements, other core areas are often changed or optimized during the ramp-up phase in addition to welding technology. This may include component geometries, material combinations, coatings, fixtures and/or system components.
Empirically, a change or modification of core areas influencing the process can affect the optimization of the welding technology. All the more important is the knowledge of the workflow in a ramp-up phase. Fundamental and indispensable in all cases is the process recording.
As the following chart illustrates, we use a wide variety of methods for this purpose.
Process Mapping
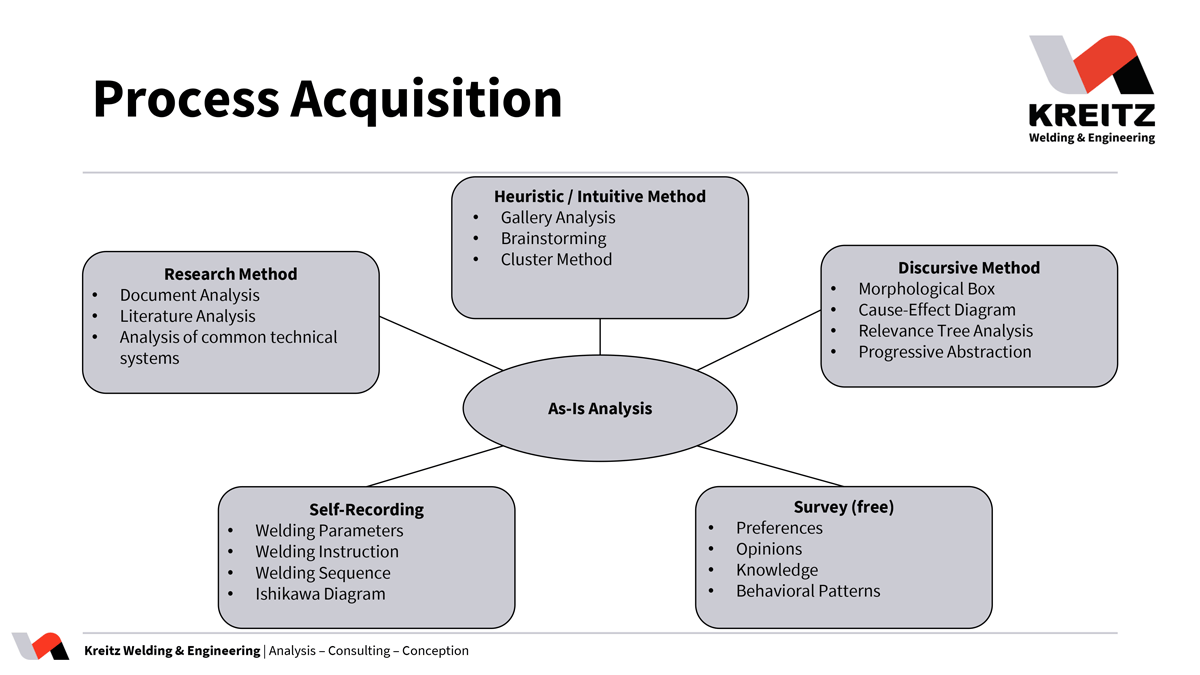
We use these methods not only during the ramp-up of series production, but likewise during optimization in series production. With slight adjustments, these also form the basis for consistent optimization and stabilization of the process.
Series production
A clear advantage for us as an external service provider in the case of ongoing series production is the fact that process errors are usually already clearly identifiable, so we can identify and resolve their causes.
High production pressure in series production is often confronted with the need for changes. In order to avoid endangering a running, but already unstable production, we carefully plan a process change to eliminate the cause, while keeping it fast to implement and reversible at any time.
The mental anticipation of the process state following a change has top priority. With increasing system complexity and a higher degree of automation, the probability increases that a change will not only eliminate the error cause, but also affect other process-relevant factors. Thus, in exceptional cases, it may occur that certain changes are primarily successful, but other process-relevant parameters are negatively affected.
While many optimization attempts end here or are nipped in the bud, we take a different approach. This is where our work actually begins. We do not only think proactively, but also take a personal interest in the success of the optimization. So, the more complex the change management process, the more appealing the task becomes for us.
From the exemplary workflow for optimizing a resistance welding process as presented below, the four phases we will go through during such a project become apparent.
Workflow
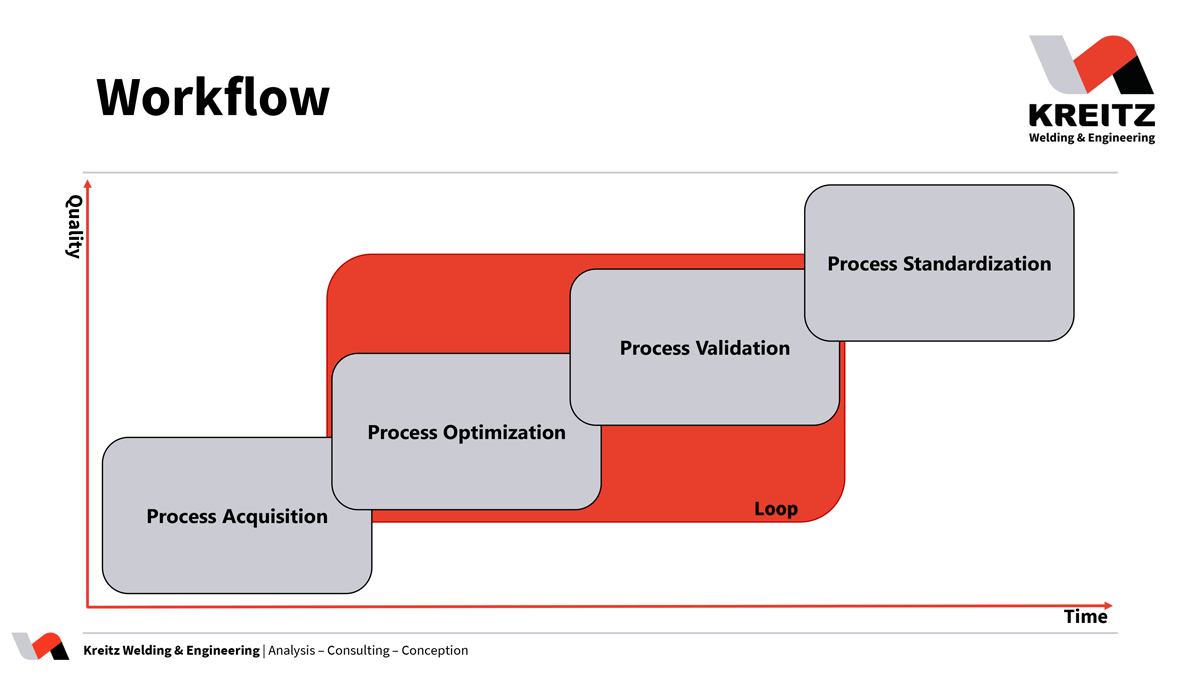
Following initial process recording, we start identifying error causes using our experience and eliminate initial sources of interference. Thus, the transition between recording and optimization is usually fluid and hardly noticeable. Thereby, great results can be achieved with little effort, especially at the beginning. According to the Pareto principle, a major part of the optimization is accomplished in a short period of time.
If, depending on the plant availability, a larger work package could then be processed continuously or with interruptions, this optimization phase is followed by a validation, generally with a defined dividing line between the optimization and validation loops.
Once an increase in product-relevant quality according to predefined criteria has been metrologically recorded, the subsequent loop can be scheduled and processed. Depending on the product and system complexity, two to three loops may be necessary to achieve the quality level required by the customer.
In this context, communication with all responsible persons in the company is crucial in order to raise awareness. Maintaining successfully established quality is one of the toughest internal challenges.
In the different scenarios, it is secondarily important to us whether we encounter an arc-guided process or resistance heating causes the materials to join. The analytical approach to process optimization, the actual workflow, remains identical in its fundamentals and is our recipe for success.
In such cases, the reversible change strategy is used to scale back the process for subsequent planning and implementation of further in-depth opitimization steps.
Whether continuous production or ramp-up: our process optimizations are visible, measurable and built for the long term.
Additional Services